Versatile, reliable, able to perform various operations with precision, robots are the preferred tools in flexible automation systems, where manufacturing is expected to change based on the changing needs of the market. Typical robot operations include loading/unloading of machines, welding, painting, all tasks in which the speed of execution increases the productivity of the factory, decreasing cycle times and exempting humans from performing such tasks in uncomfortable conditions. The spread of the production paradigms of Industry 4.0 has given renewed importance to the use of robots, as highly digitalised machines. Alongside traditional industrial manipulator systems, mobile robots (AGV, AMR, LGV) are of increasing importance in industrial logistics and, in general, in applications relating to material flow and transport. Robotics also benefits from the evolution of other production technologies, in particular additive manufacturing, where the robot manipulator is equipped with a tool for deposition of material or is integrated with 3D printers to improve its productivity. Collaborative robotics is a key enabling technology for safe operation in mixed human‒robot environments.
INVERSE

- INteractive robots that intuitiVely lEarn to inVErt tasks by ReaSoning about their Execution
- January 2024 ‒ December 2027
- 7,999,873.50 €
- website
MELODY
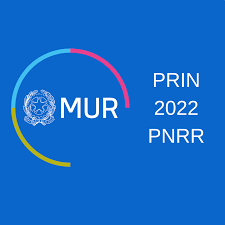
- Multi robot collaborativE manipuLation suppOrting DisassemblY tasks
- November 2023 ‒ November 2025
- 220,921,17 €
foAIming
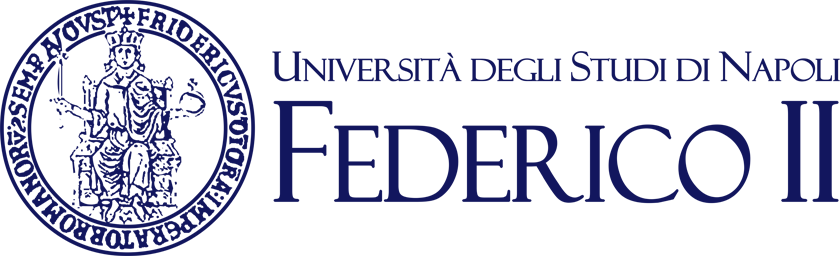
- Artificial intelligence and robotics in polymer foaming
- April 2021 ‒ March 2023
- 39,795 €
TOP
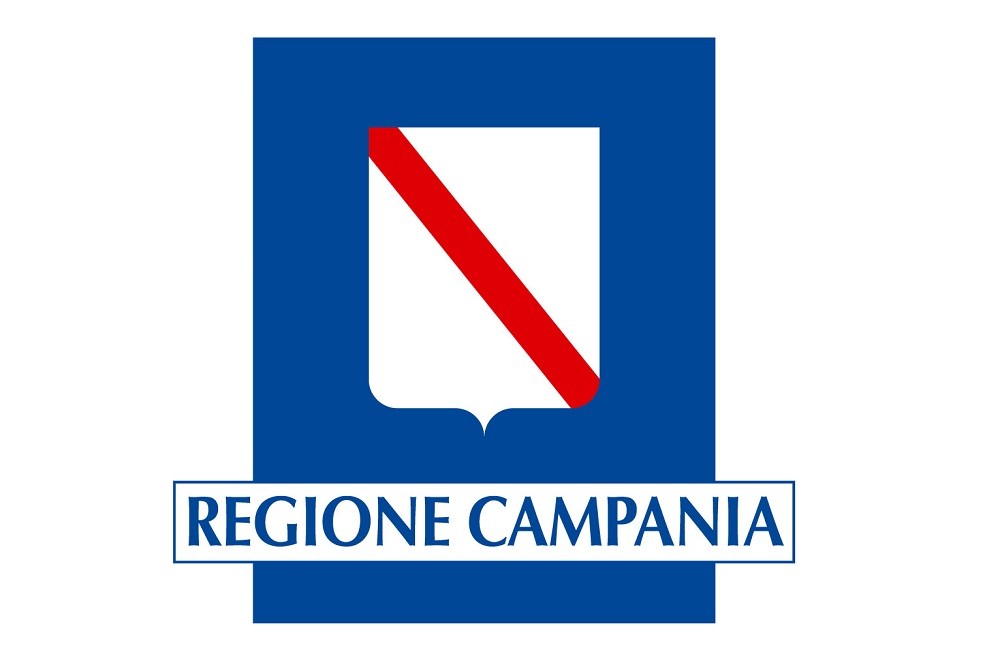
- New Engineering & Manufacturing Enhanced System Innovation
- January 2020 ‒ December 2023
- 3,500,000 €
ICOSAF
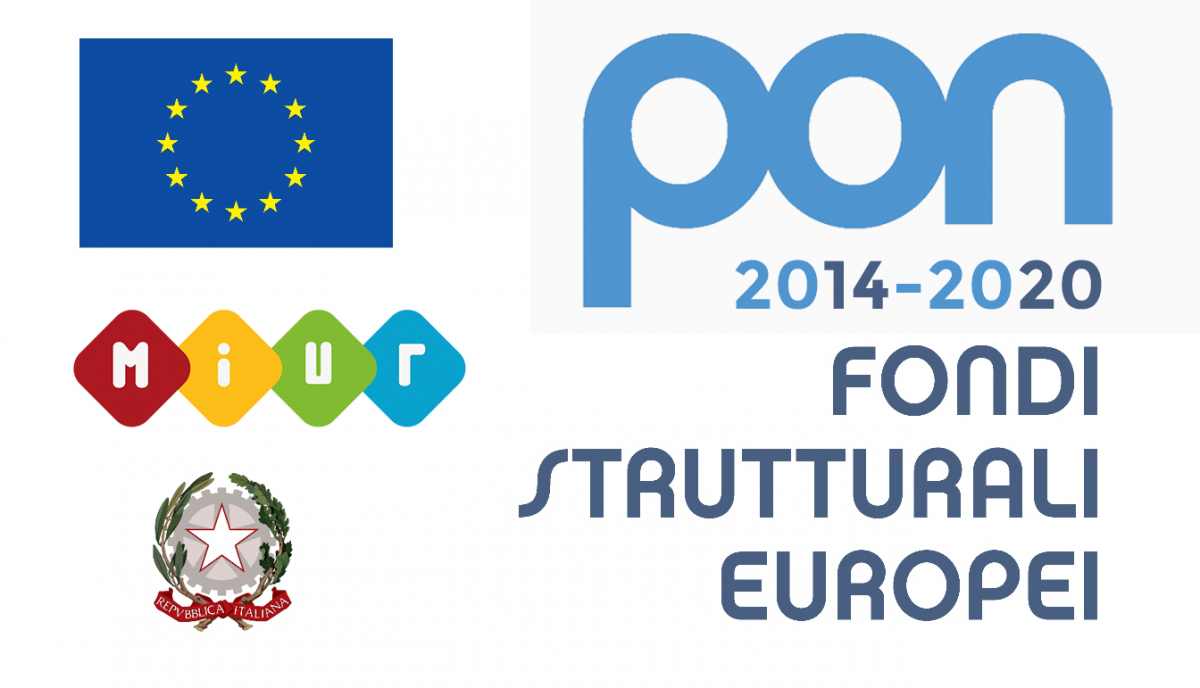
- Integrated and collaborative systems for the intelligent factory
- September 2018 ‒ March 2021
- 4,927,079 €
ROMOLO

- Modular robots for hospital logistics
- June 2017 ‒ December 2019
- 853,617 €
The project is focused on modular robotic systems capable of working in hospitals by performing different tasks in the logistics. Proper systems and components are to be developed with appropriate interfaces to users and with hospital networks and systems. These technologies can make more efficient hospitals and have a positive impact on patients and staff. The proposed robotic system consists of an omnidirectional mobile base capable of transport, after a suitable coupling, various accessory modules, e.g. trolley with laundry, system drug dispenser, telepresence vision system, through the wards of a hospital.
REFILLS
- Robotics Enabling Fully-Integrated Logistics Lines for Supermarkets
- January 2017 ‒ December 2020
- 3,692,850 €
- website
While online grocery stores are expanding, supermarkets continue to provide customers with the sensory experience of choosing goods while walking between display shelves. Retail and logistics companies are committed towards a shopping experience more comfortable and exciting while, at the same time, using technology to reduce costs and increase efficiency. REFILLS is to improve logistics in a supermarket thanks to mobile robotic systems in close and smart collaboration with humans, addressing the main in-store logistics processes for retail shops such as smarter shelf refilling. Information on the articles is exploited to create powerful knowledge bases, used by the robots to identify shelves, recognize missing or misplaced articles, handle them and navigate the shop. Reasoning allows robots to cope with changing task requirements and contexts, and perception-guided reactive control makes them robust to execution errors and uncertainty.
STEPFAR

- Development of Eco-Compatible Materials and Technologies, Drilling and Cutting Processes, and Robotic Assembly
- April 2014 ‒ June 2017
- 4,436,055,75 €
In aeronautical industry the reduction of the weight of the aircraft is becoming an increasingly important aim both for environmental requirements (lower emissions) and contraction of the management costs (lower fuel consumption). For this reason new structural architectures through the use of innovative materials and technologies have been developing. Innovative processes which will be developed in this project are drilling and cutting through a laser source of aluminum alloys, and drilling via machining, using collaborating anthropomorphic robots, of hybrid aluminum/composite stack-ups and their assembly. Moreover, static and dynamic characterization will be carried out. In addition materials and processes with low environmental impact (elimination / reduction of hazardous substances from the painting process and energy-saving products used: water, detergents, paints, thinners) will be selected and developed for the treatment of aircraft surface to ensure protection from aggressive factors comparable or higher to one offered by materials and processes currently used and in compliance with the certification requirements of aeronautical structures. Painting processes and surface protection treatments will be also studied to have innovative features, in addition to be eco-compatible, in order to reduce the specific fuel consumption of the aircraft using aerodynamic coatings, layers and weight optimization of the employed coatings. Furthermore, assembly techniques for hybrid aeronautical components of composite/aluminum will be developed in order to facilitate couplings without shims through the exam of coupling surfaces and adequate geometric correction techniques of parts.
RODYMAN
- Robotic Dynamic Manipulation
- June 2013 ‒ May 2019
- 2,496,600 €
- website
The goal of the RODYMAN project is the derivation of a unified framework for dynamic manipulation where the mobile nature of the robotic system and the manipulation of non-prehensile non-rigid or deformable objects are taken into account. Novel techniques for 3D object perception, dynamic manipulation control and reactive planning will be proposed. An innovative mobile platform with a torso, two lightweight arms with multi-fingered hands, and a sensorized head is to be developed for effective execution of complex manipulation tasks, also in the presence of humans. Dynamic manipulation is tested on an advanced demonstrator, i.e. pizza making process, which is currently unfeasible with the prototypes available in the labs. The research results to be achieved in RODYMAN contribute to paving the way towards enhancing autonomy and operational capabilities of service robots, with the ambitious goal of bridging the gap between robotic and human task execution capability.
DEXMART
- Dexterous and Autonomous Dual-Arm/Hand Robotic Manipulation with Smart Sensory-Motor Skills: A Bridge from Natural to Artificial Cognition
- February 2008 ‒ January 2012
- 6,300,000 €
- website
The DEXMART project is focused on artificial systems reproducing smart sensory-motor human skills, which operate in unstructured real-world environments. The emphasis is on manipulation capabilities achieved by dexterous, autonomous, human-aware dual-arm/hand robotic systems. The goal is to allow a dual-arm robot including two multi-fingered redundant hands to grasp and manipulate objects with different shape, dimension and weight. Manipulation takes place in an unsupervised, robust and dependable manner so as to allow the robot to safely cooperate with humans for the execution of given tasks. The robotic system has: to possess the ability to autonomously decide between different manipulation options, to properly and quickly react to unexpected situations and events such as changes in human cooperation, to acquire knowledge by learning new action sequences so as to create a consistent and comprehensive manipulation knowledge base through an actual reasoning process.