FIR Lab (Field and Industrial Robotics Laboratory) is the main experimental facility of the PRISMA Team devoted to design, development and testing of innovative robotic solutions. The lab is equipped with fast prototype machines, e.g. 3D printers and CNC, and several manipulation robots employed for research in field and industrial robotics.
Venue: Department of Electrical Engineering and Information Technology, University of Naples Federico II, bldg. 5/A, via Claudio 21, 80125 Naples
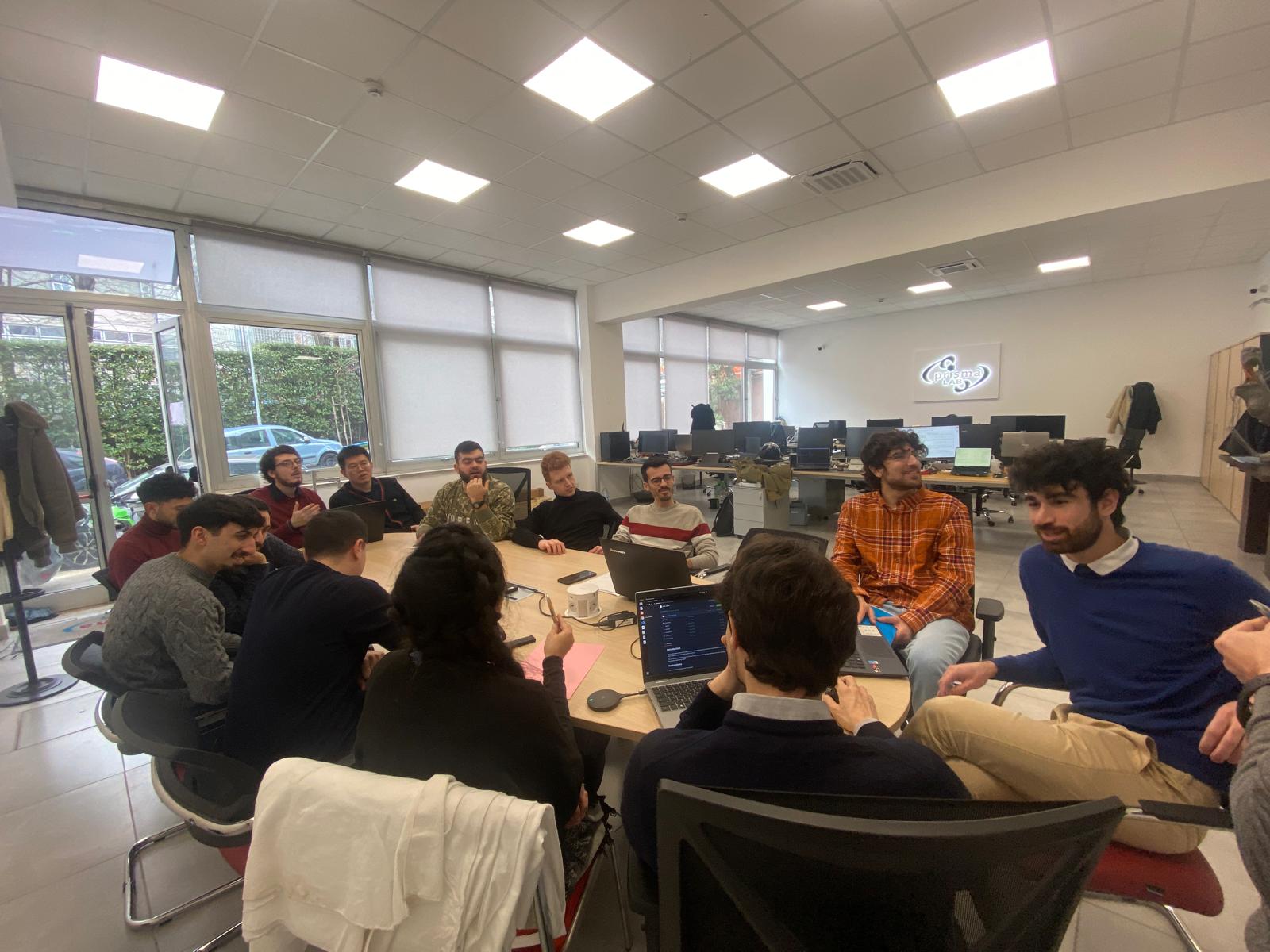
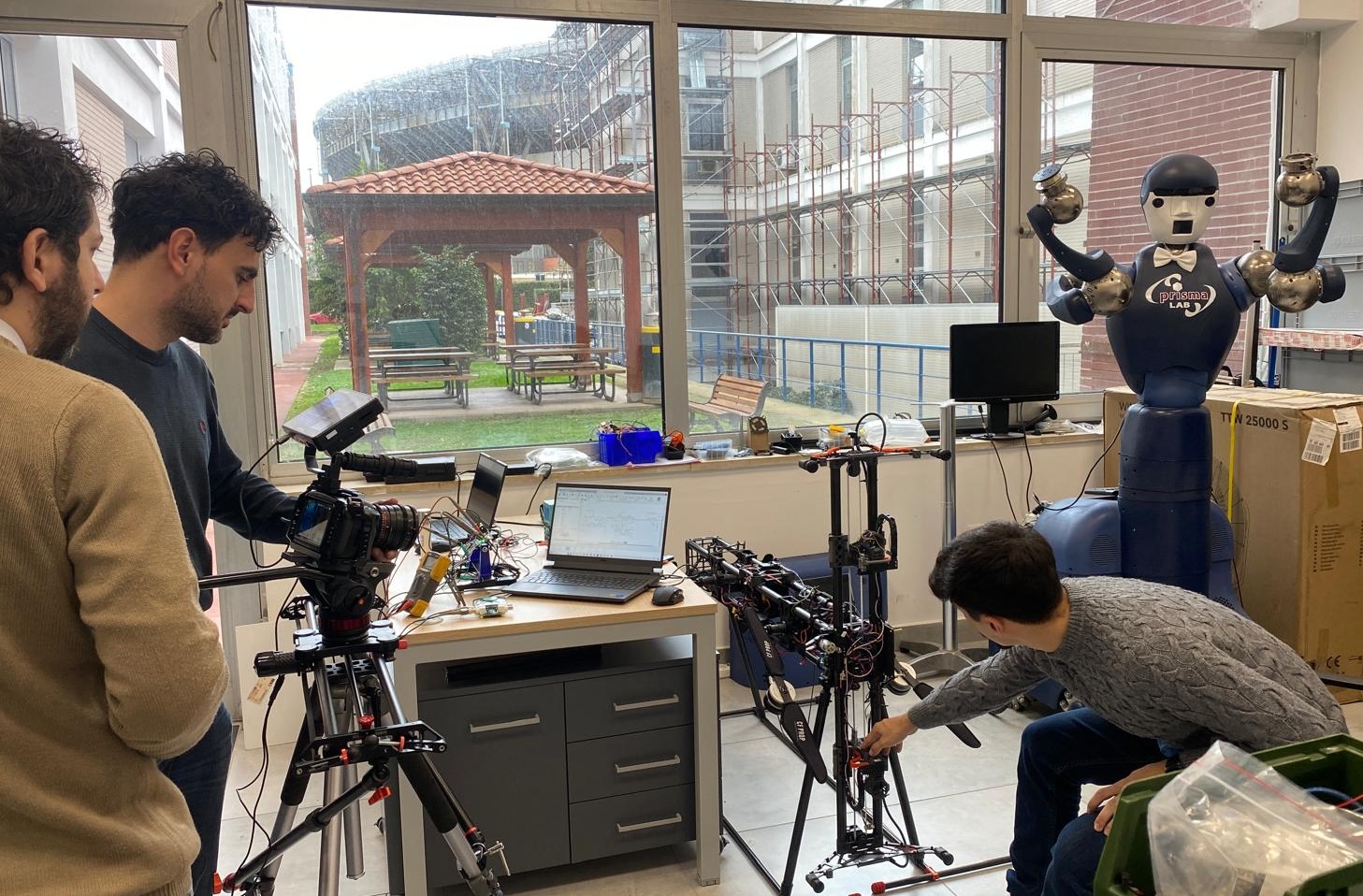
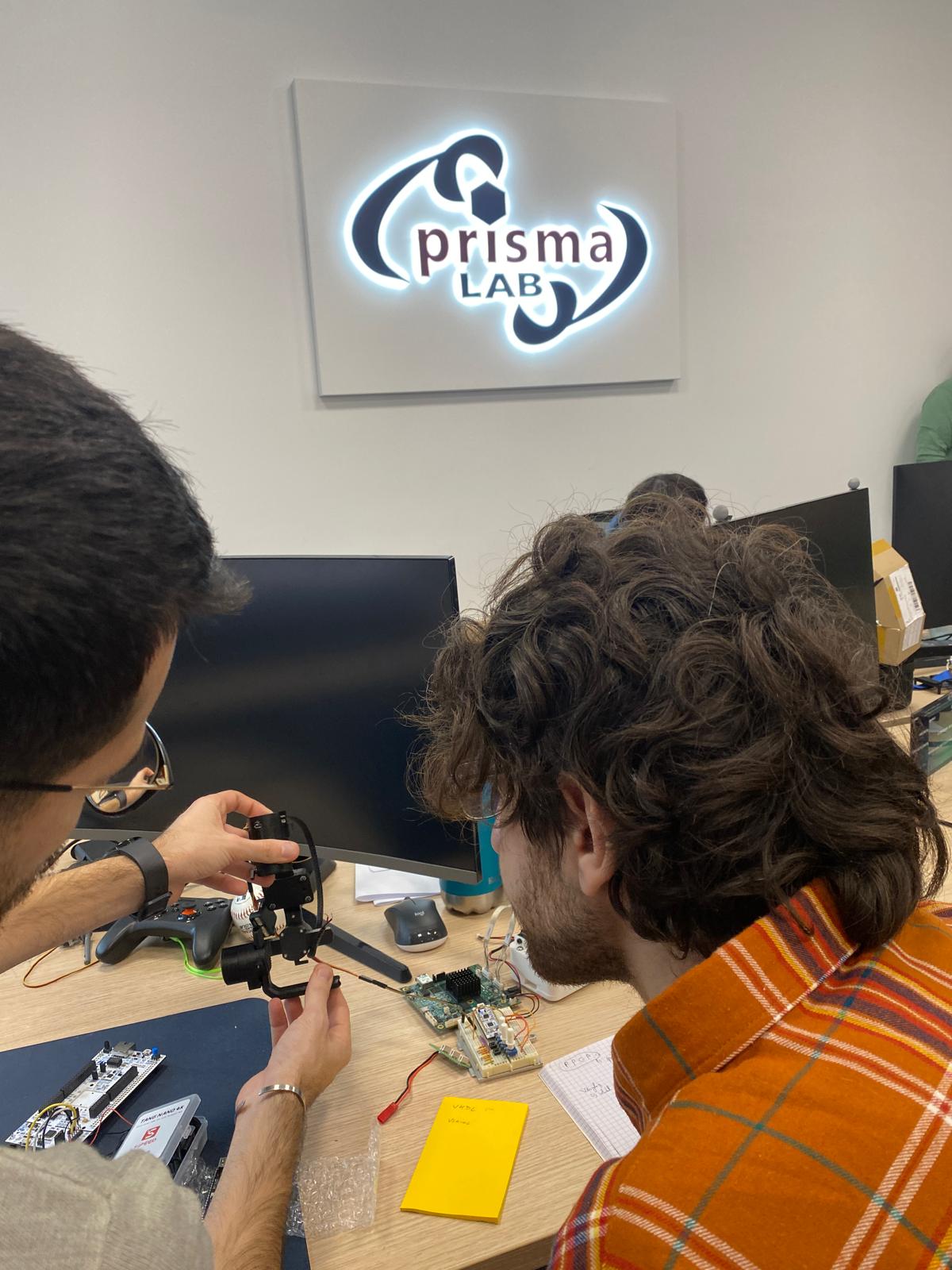
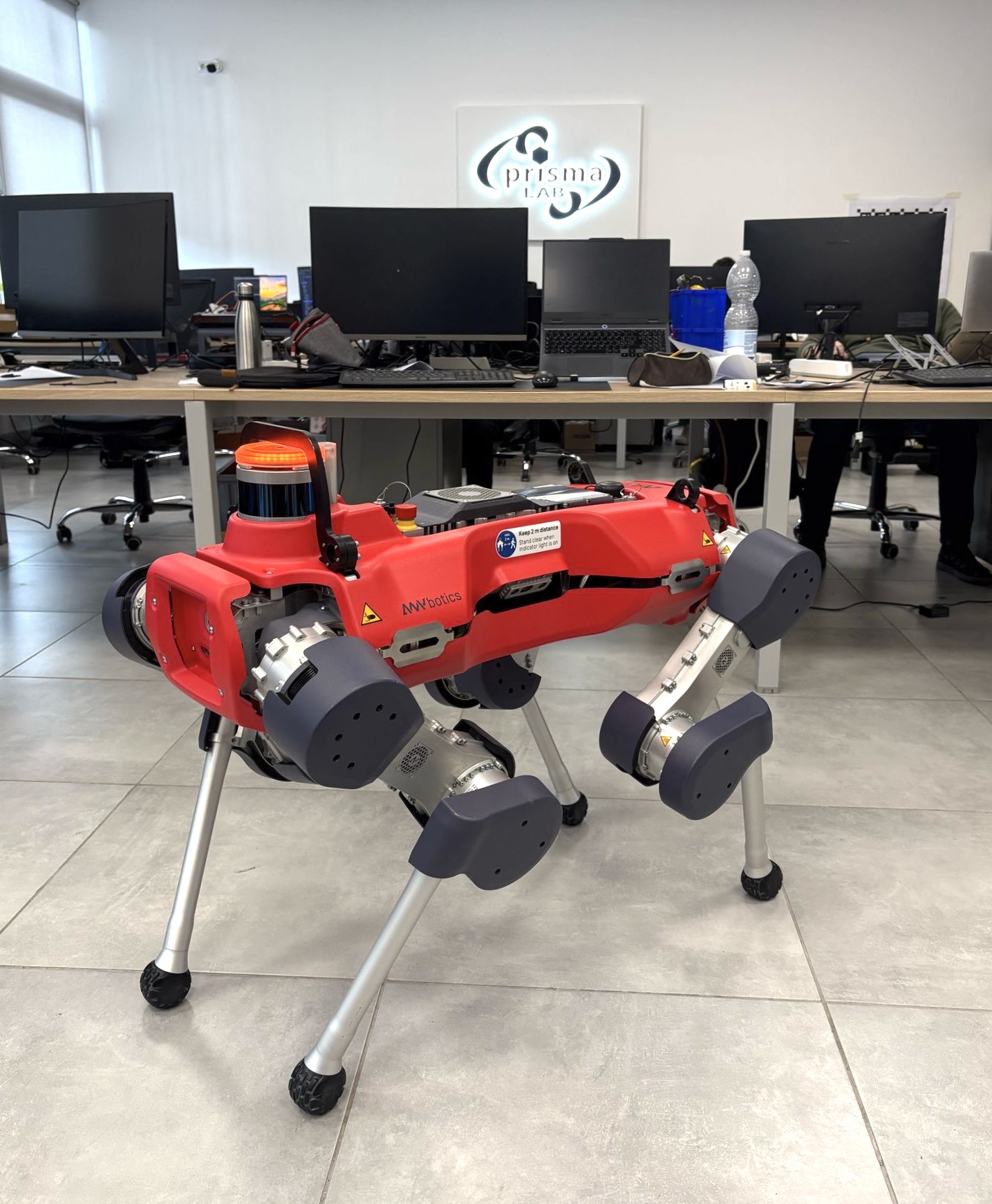
- Quadruped robot with 12 degrees of freedom
- Key dimensions: 930 mm of length, 530 mm of width, 800 mm of height
- 3-degree-of-freedom legs (2 DOF at the hip, 1 DOF at the knee)
- Compact and mechanically compliant ANYdrive actuators
- 50 kg of mass, up to 15 kg of carried payload
- 360° perception of the near environment and obstacles within 2 meters enabled by 6 depth cameras, 360° perception of obstacles within 100 meters enabled by the 3D LiDAR
- Two 8th gen Intel Core i7-based PCs for real-time locomotion and navigation functions
- Built in Wi-Fi module for communication with an external PC
- Swappable Li-ion battery, UN 38.3 certified 932.4 Wh, IP 67
- Capable of reaching speeds up to 1.3 m/s, to climb steps up to 250 mm, to cross gaps of up to 300 mm and to walk on slopes of up to ±30°
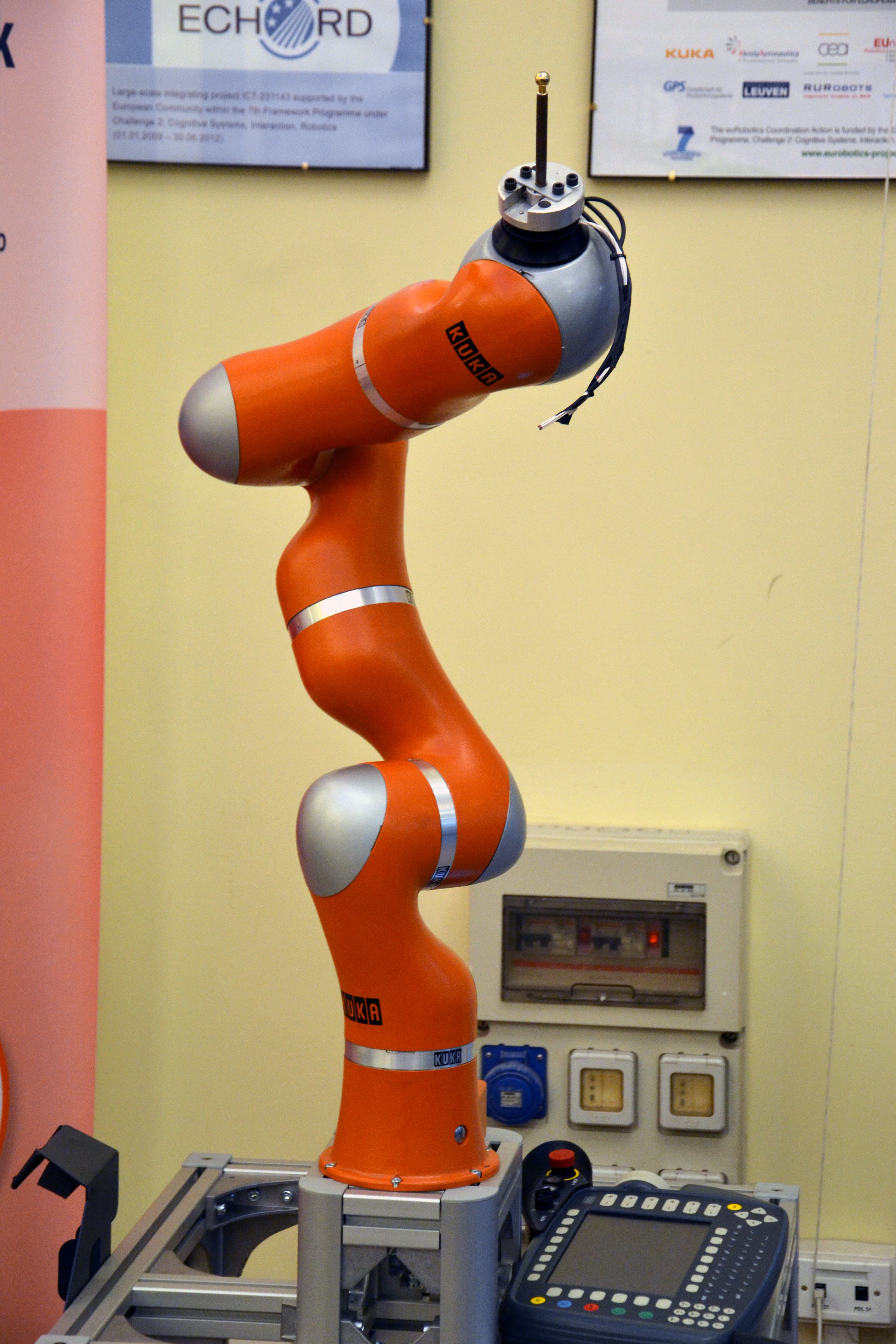
- 7 kg payload
- 7-degrees-of-freedom robot
- In-line wrist variant
- Mounting flange DIN ISO 9409-1-A 50
- Any mounting position available
- 0.05 mm repeatability (ISO 9283)
- KR C2 lr controller
- 16 kg weight (excluding controller)
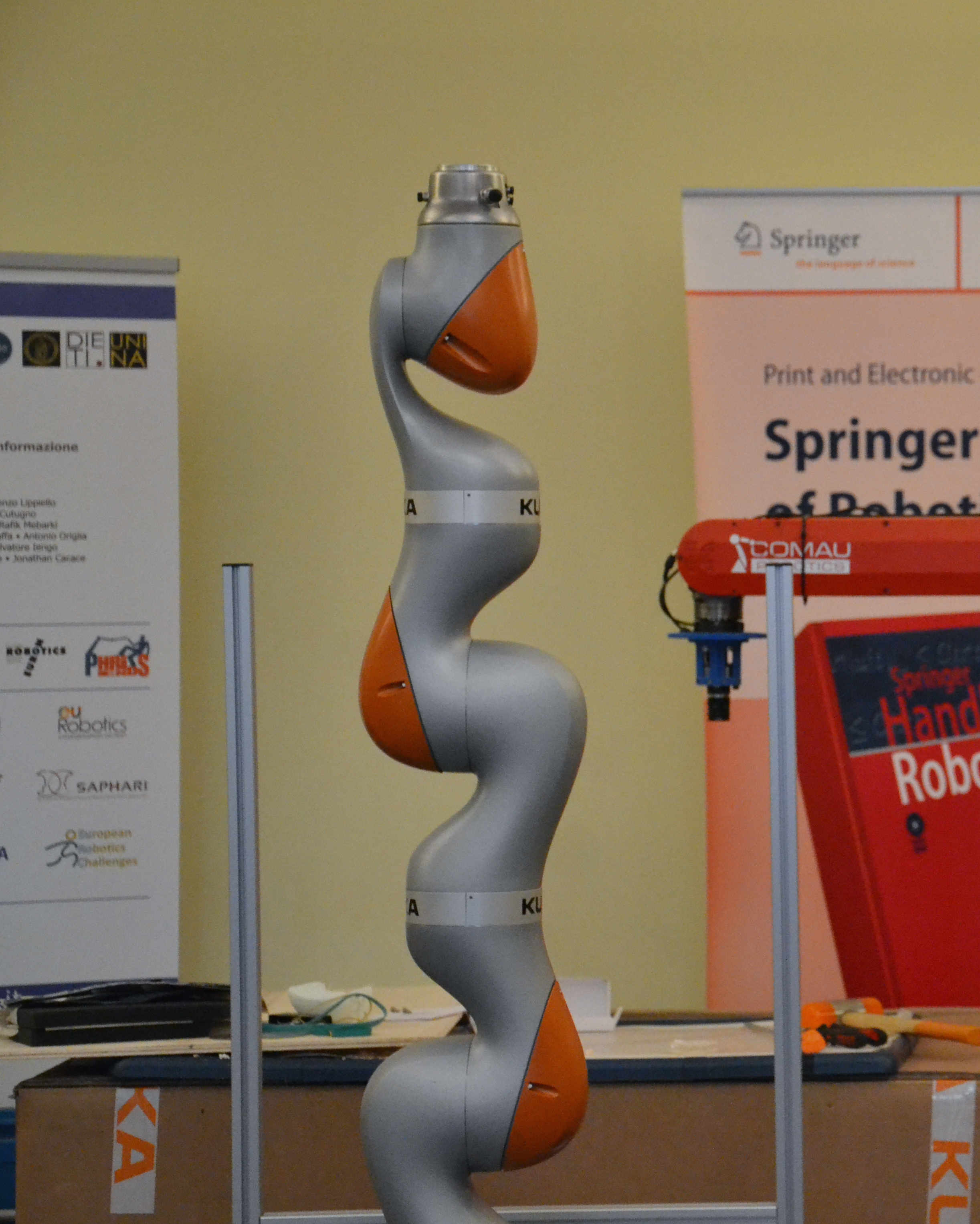
- 7 kg payload
- 7-degrees-of-freedom robot
- In-line wrist variant
- Mounting flange DIN ISO 9409-1-A 50
- 0.1 mm repeatability (ISO 9283)
- KUKA Sunrise Cabinet
- 22 kg weight (excluding controller)
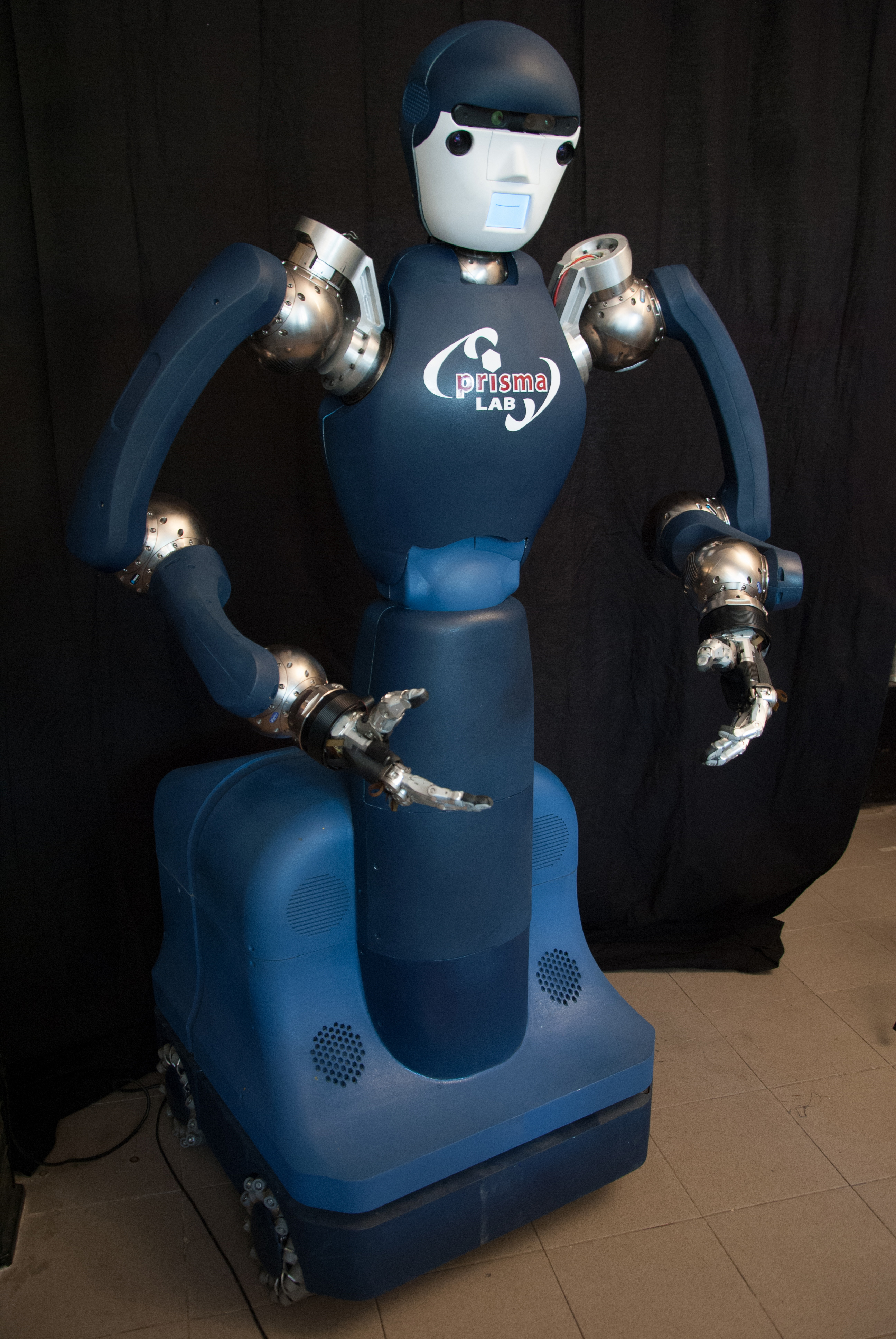
- Humanoid-like 21-degree-of-freedom robot
- Omnidirectional mobile platform
- Two SCHUNK LWA 4P arms with 6 degree of freedoms each
- 7th degree of freedom provided by SCHUNK PRL-100 integrated into shoulder
- Two motors actuating torso and one motor for pan-tilt neck
- QNX-based PC for real-time and low-level control of motors and implementation of safety procedures
- Linux-based PC used for perception and high-level planning and control algorithms
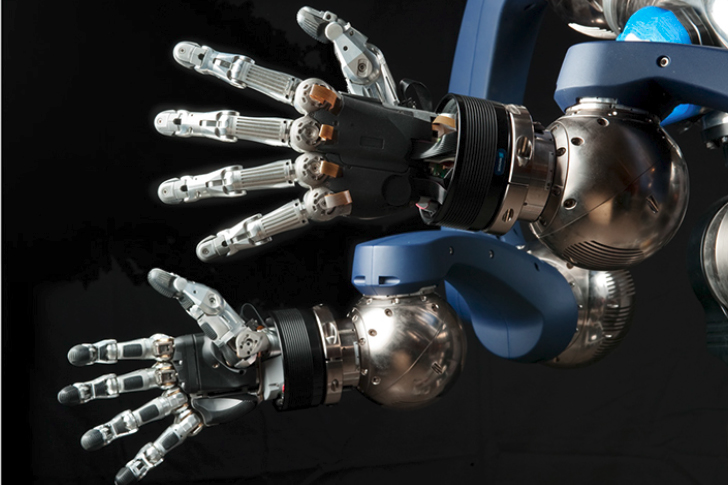
- Anthropomorphic structure 1:1 ratio to the human hand
- 20 joints and 9 degrees of freedom
- Low energy consumption at 24 V DC
- Integration of control, regulator and power electronics in the wrist/li>
- ROS driver available
- RS-485 interface
- Easy connection with market-standard industrial and lightweight robots
- 1.3 kg weight
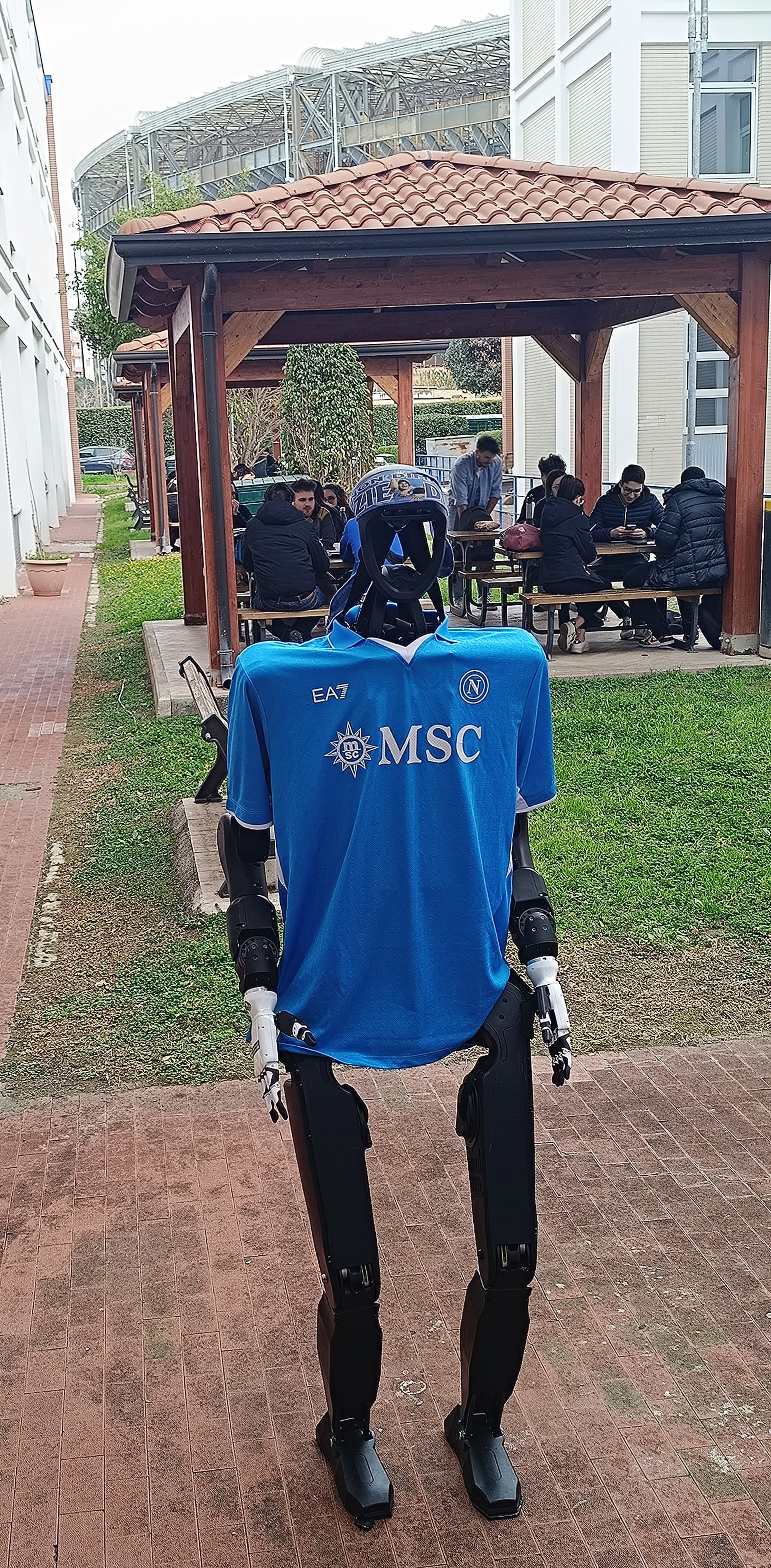
- Humanoid robot with 27 degrees of freedom
- Key dimensions: 1788mm × 510mm × 287mm
- 7-degree-of-freedom arms (each arm with 3 DOF at the shoulder, 1 DOF at the elbow, 3 DOF at the wrist)
- 6-degree-of-freedom legs (each leg with 3 DOF at the hip, 1 DOF at the knee, 2 DOF at the ankle)
- High-torque motors delivering up to 120 N·m for arms and 360 N·m for legs
- 360° perception enabled by 3D LiDAR and depth camera
- Intel Core i5-based PC for real-time platform functions
- Optional Nvidia Jetson Orin NX for advanced user development
- 15 Ah (0.864 kWh) battery with a maximum voltage of 67.2 V
- Permanent magnet synchronous motors (PMSM) with high-speed, low-inertia design
- Industrial-grade cross roller bearings for precision and load handling
- Capable of reaching speeds up to 2 m/s
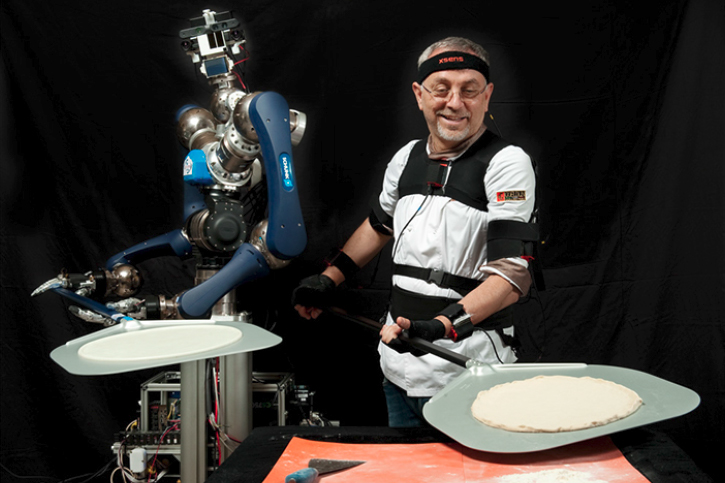
- MTx inertial and magnetic measurement units
- 3D gyroscopes, 3D accelerometers, and 3D magnetometers
- Body worn sensors on shoulders, sternum, head, arm, forearm, and hand
- Two Xbus Masters handle the wireless communication with the PC and synchronize all sensor
- Real-time frequency of maximum sampling rate of 120Hz
- MVN Studio Software
- 1.9 kg weight